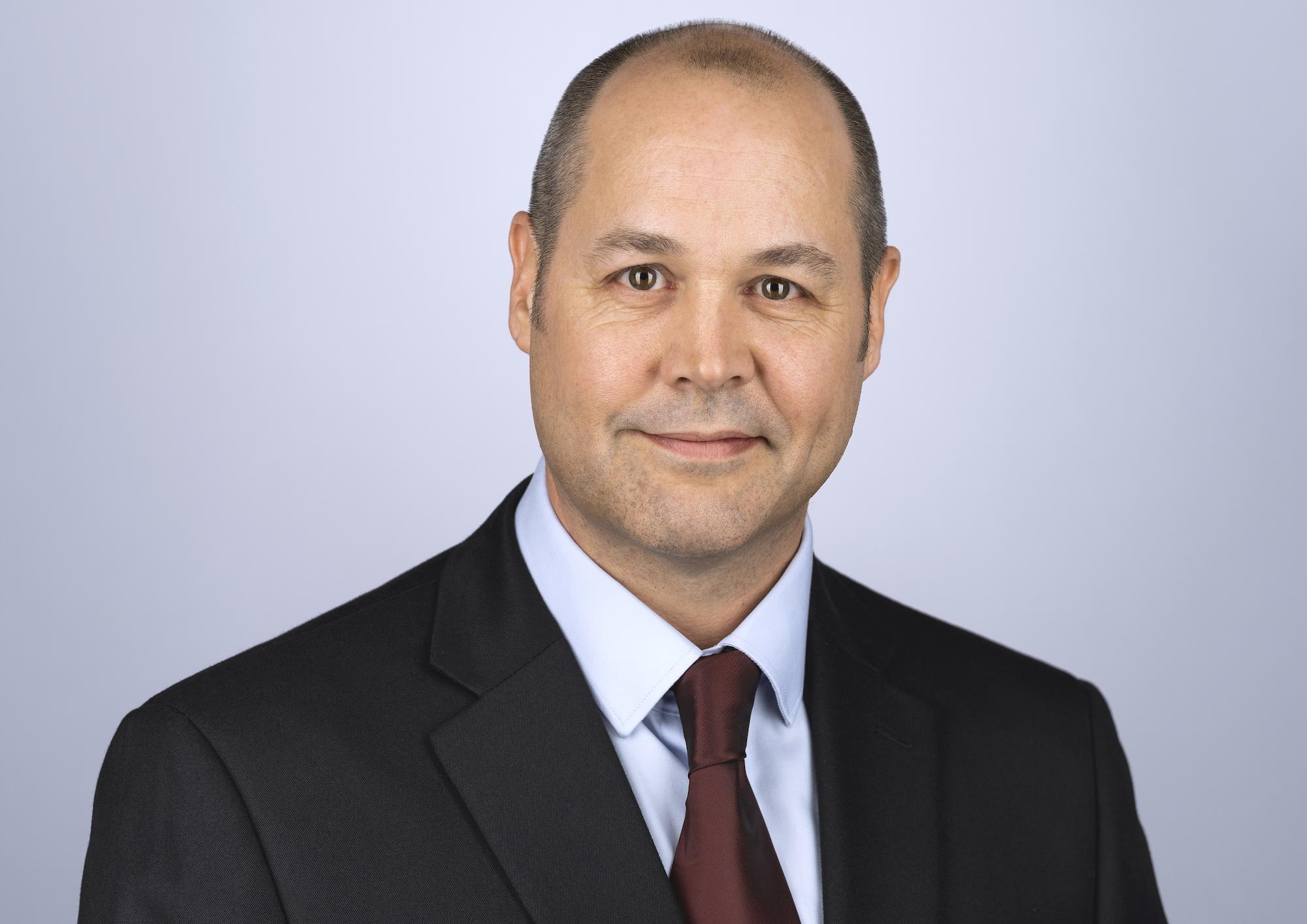
Chris Smeeton,
CEO, Argosy
Argosy have over 16,000 SKU codes listed on our operating system. These are supplied to us by vendors from across the globe, all of which have been affected to some degree by Covid restrictions and global shortages on raw materials, plus the knock-on effect that the war in Ukraine is having on the movement of goods across that geography.
Fortunately, Argosy tends to favour vendors that manufacture their products in the UK, meaning that transit times are generally favourable. This or course also means that we are protected from fluctuations in exchange rates.
The way we place our purchase orders for these products has had to change to secure production space and allow for extended lead-times caused by raw materials shortages. We now often place holding orders or call off orders with our suppliers, that we ‘draw down’ to align with our usage. This not only secures production space but also allows us to maintain significant stock holdings, whilst managing cash flow in line with the wider objectives of the business.
For goods manufactured elsewhere, we must accept that longer lead-times are now an accepted part of the current landscape. Here, honest and accurate communication between us and our suppliers and through to our customers is key. Fortunately, these global challenges are so high profile that having such discussions with customers are accepted and trusted and therefore there is not a negative impact on the reputation of the respective companies. In fact, we find this honest dialogue demonstrates our key strength of supply-chain management.
This is not to say that we can’t be caught out. We recently experienced a Covid breakout at the factory of one of our suppliers which set back production time on a key product required for a project that had a critical timeframe. Fortunately, our relationship with that customer was strong enough to cope with this but it does make life complicated and uncomfortable for all involved.
Over many years we have championed the need to see our suppliers as true ‘partners’ and now more than ever, we are proving how we can work together to manage these challenges.
Of course, the current situation is also having an impact on the human element of our business. It has been difficult and expensive to travel to meet with suppliers and customers over the last few years, especially across borders with changeable restrictions. Dialogue has had to take place across
virtual platforms and going forward we believe supplier engagement at trade shows will be as important a part of trade shows as the customer contact.
Recruitment and training are also being affected by the current situation. Many staff now work from home some of the time as we adopt hybrid working. This means the time we do spend together is critical for maintaining our team ethos. We also have management meetings each week to discuss issues and plans for the week so that we can share ideas and plan accordingly.
Overall, we see that forward planning, leaner processes and honest communication are the key to overcoming the difficulties being faced.